Company News
11/21/2023
VWAC’s High-Voltage Battery System Rolls Off Production Line – A Crucial Step towards EV Production in Anhui
- New high-voltage battery system at Volkswagen (Anhui) Components Co., Ltd. (VWAC) will supply Volkswagen Anhui’s MEB electric vehicles
- Under Group’s ‘goTOzero’ mission and ‘Zero Impact Factories’ goal, VWAC is committed to utilize 100% renewable electricity by 2025
- Significant milestone for Volkswagen Group’s electrification transformation and its “In China, for China” strategy
- Olaf Korzinovski: “With the first high-voltage battery system rolling off the production line at VWAC, Volkswagen Group Components China has shown its dedication to locally developing and producing top-notch backbone components for our electric vehicles.”
- Jan Kasper Kuipers and Oliver Harmann: “The start of production has proven VWAC as a reliable supplier to produce high quality battery systems. Today’s milestone is based on true teamwork. We would like to express our gratitude for the support from the local government, partners, and the Group.”
Volkswagen (Anhui) Components Co., Ltd. (VWAC), Volkswagen Group’s first 100% owned battery system plant in China, starts production of its first high-voltage battery system. The battery system is a crucial component for Volkswagen Anhui’s MEB electric vehicle production. This is the latest milestone in the Group’s strategic development of Hefei as a high-tech intelligent connected vehicles (ICV) hub and marks another major achievement for the Group’s ‘In China, for China’ strategy.
Olaf Korzinovski, Executive Vice President of Volkswagen Group China, responsible for Components, Logistics and QA, said: “Volkswagen Group Component China is actively driving our transformation towards a new era of intelligent, connected vehicles, in China, for China. VWAC serves as the powerhouse of battery production and is a vital part of our future development. With the first high-voltage battery system rolling off the production line at VWAC, Volkswagen Group Components China has shown its dedication to locally developing and producing top-notch backbone components for our electric vehicles.”
Jan Kasper Kuipers, VWAC’s General Manager of the Technical Department, and Oliver Harmann, General Manager of the Commercial Department, gave a joint introduction to the history of the project during a ceremony marking the occasion. “The start of production has proven VWAC as a reliable supplier to produce high quality battery systems,” they said. “Today’s milestone is based on true teamwork. We would like to express our gratitude for the support from the local government, partners, and the Group.”
VWAC is the first battery system plant wholly invested by Volkswagen Automatic Transmission (Tianjin) Co., Ltd. With an initial annual capacity of 150,000 to 180,000 high-voltage battery systems, VWAC will power Volkswagen Anhui’s all-electric vehicles based on the Group’s MEB platform.
The newly produced battery system consists of multiple cell modules, cell management controller, battery management system, and connector strips. 96% of the components required for battery production are supplied locally.
Consistent with the Group’s vision and dedicated investment in a digitized manufacturing process, the production, assembly and testing of the battery systems will integrate cutting-edge technology and automation at each stage.
In particular, the entire production process is covered by automatic line feeding technology. Through a combination of automated guided vehicles (AGV), high-precision intelligent cameras, and industrial robots, VWAC can achieve just-in-sequence (JIS) logistics and accurate parts processing, ensuring production stability and the quality of products. The quality lab also boasts a water cutting machine, laser radar, and 3D coordinate measuring machine (CMM) equipment, all of which improve the efficiency of product analysis while meeting Volkswagen Group’s stringent quality standard.
At the same time as ensuring production efficiency, the company also attaches great importance on the working environment and employee health and safety. For example, the specially designed ergonomic tilt conveyor on the assembly line allows every operator to work in comfortable position.
VWAC is also poised to spearhead the production of the Group’s cell-to-pack (CTP) battery packs using unified cells developed in cooperation with Gotion High-Tech.
Covering an area of 45,000 square meters, VWAC sits next to the production facilities of Volkswagen Anhui, Volkswagen’s first majority-owned joint venture for all-electric vehicles. The plant’s construction was completed within a record 12 months, demonstrating ‘Hefei speed’ “.
The company strives to serve as a model for sustainable manufacturing practices and contribute to sustainable development of the Group.
Since its establishment, VWAC has been fully aligned to the Group’s ‘goTOzero’ mission and the goal of creating ‘Zero Impact Factories’. VWAC has already adopted a geothermal heat pump system that covers 100% of the office and auxiliary building areas, which is estimated to save around 900MWh of energy per year. A range of measures are also being implemented to achieve 100% green electricity usage.
The successful production launch at VWAC provides a significant boost for new energy vehicle components supply, marking a major milestone in the Group’s investment in Hefei. This achievement injects new energy and vitality into the industry ecosystem and local economy.
零部件公司首套高压电池系统正式下线-2.jpg)
执行副总裁,零部件、物流与质保部负责人康诺一致辞-1.jpg)
零部件有限公司技术总经理库阳(左)和商务总经理韩浩文(右)致辞-1.jpg)
零部件有限公司-1.jpg)

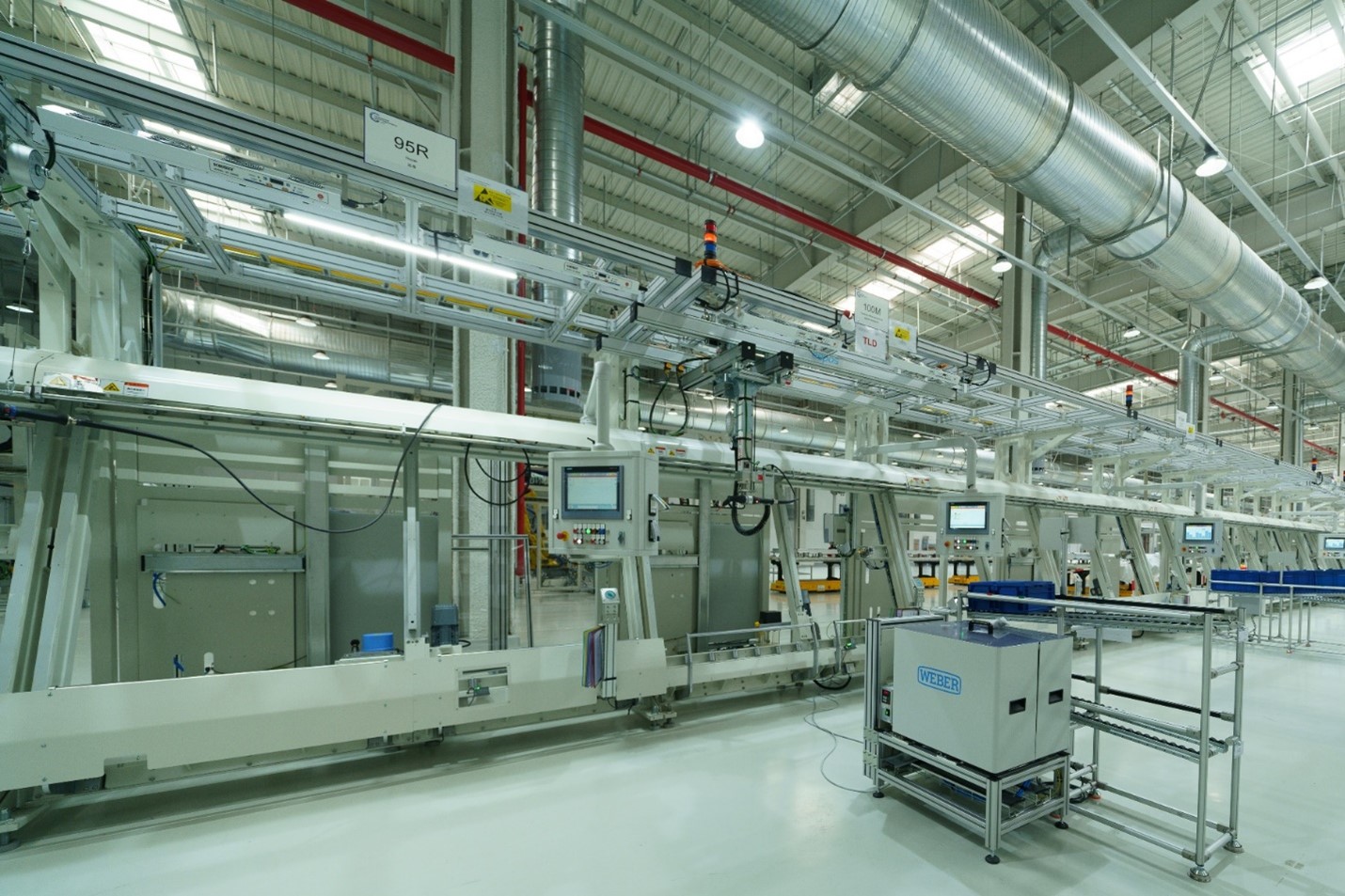
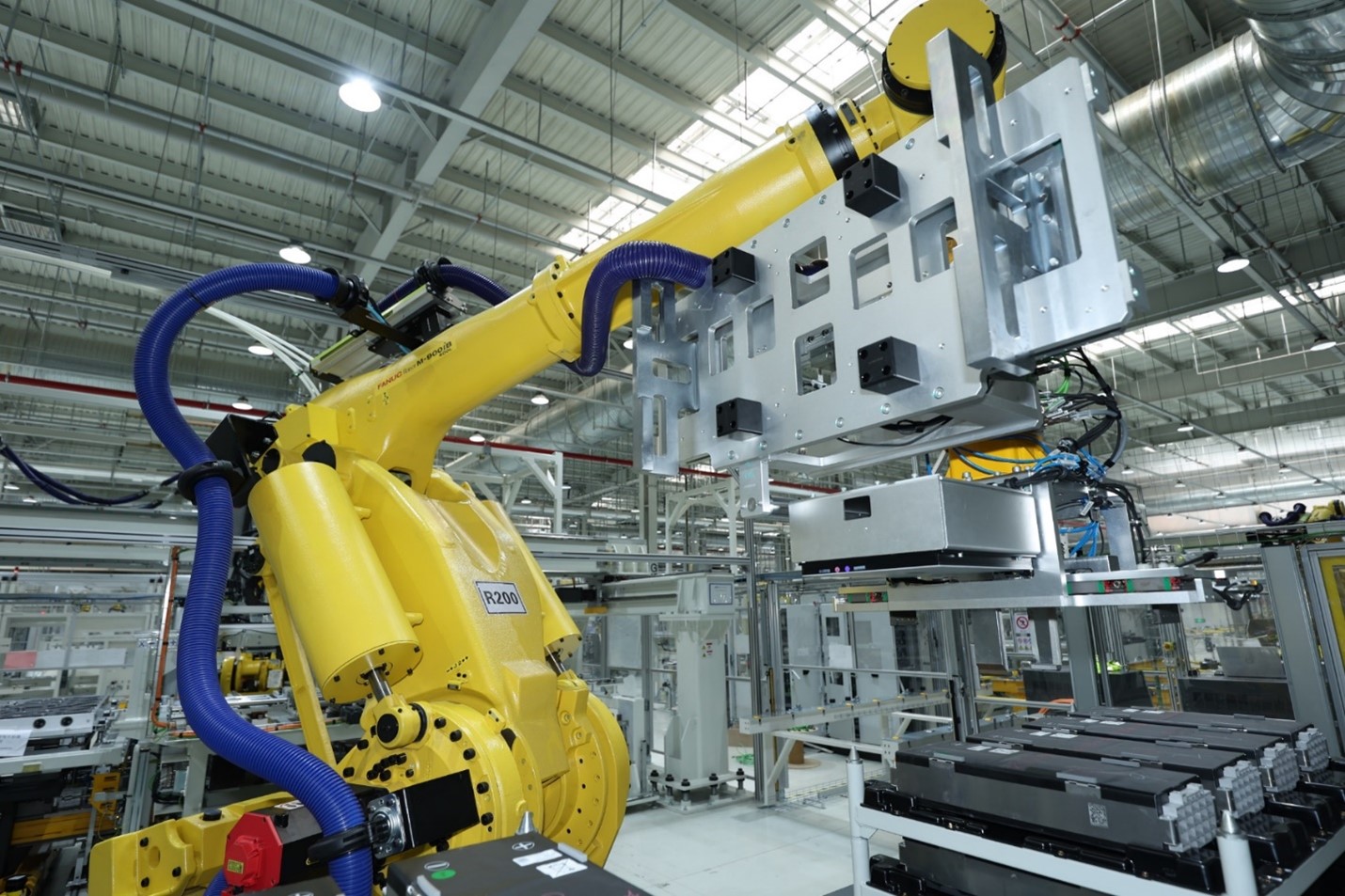